Sean Mills makes all the pots at Clearwater Ceramics in Gloucestershire. While many potters like to produce a specific range of pots Sean prefers to experiment with different styles and ideas across all different clay types. Currently he produces pots in porcelain fired to 1260 degrees centigrade and in earthenware which fires at 1100 degrees. Almost all his pots are thrown.
As a retired person Sean is in the fortunate position of being able to donate all revenues from pot sales to help maintaining water wells in rural Sierra Leone. Sean is a Trustee of Rory’s Well and currently has responsibility for 124 wells producing fresh water for 17,000 people who would otherwise have to rely on polluted water from rivers and bogs. By buying one of Sean’s pots you not only get something which will delight you for years but you contribute to people’s health in a material way.
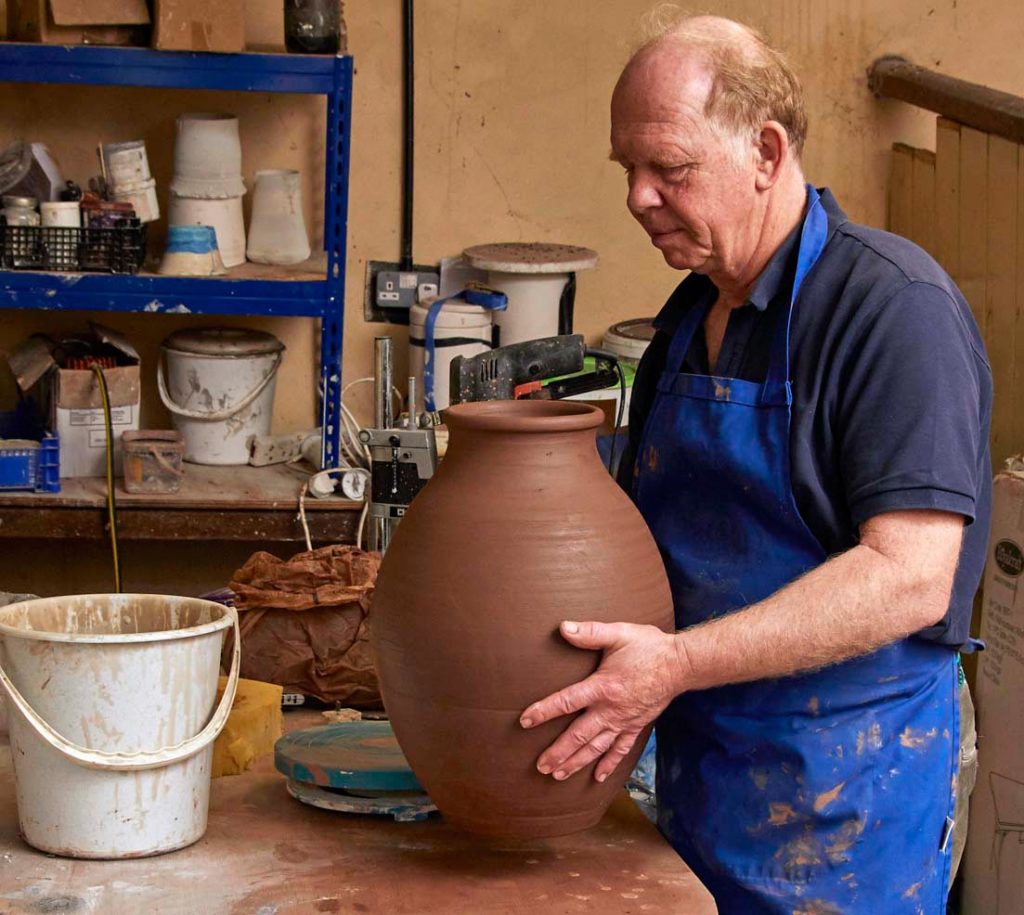
The Process
Throwing is addictive. Clay has a spirit all of its own, which grows like a live animal in the hands of the potter. From the physicality of the cantering and thinning processes to the slightest of touches that is required to form the lips and curves of porcelain pots, clay has a sensuality unlike any other medium. Added to that, the variety that is offered by different clay bodies, slips, glazes and firing processes and you have a lifetime of experimentation and interest that can never dull.
Wedging
Three processes are required to make a raw pot. First the clay must be wedged. This involves needing it, in much the same way as one would need bread. This eliminates the air bubbles which would otherwise crack the pot when fired in the kiln, and makes the clay entirely consistent so that when throwing, it has a consistent friction against the potter's hands.
Throwing
After wedging the pot is thrown. What I love about this is that the art of throwing has been around for thousands of years, using essentially the same basic tools. The potter aims to make the walls of the pot the same thickness from top to bottom and to achieve a purity of line without overworking the form which will 'squeeze the life out of it'. Throwing gives an immediacy to the creative process which you cannot get from hand building. By combining different sections you can still get a complicated final form if desired.
Turning
Finally the pot is turned when leather hard to remove any excess clay at the base and to carve a footing into the base of the pot if desired. Thereafter slips can be added, particularly to earthenware pots to give colour and designs before the dry pot is bisque fired to around 1000 degrees centigrade. After that the pot is glazed and then re-fired to produce the finished item.